QA/QC Intern – Mechanical Inspection
Actively participated in QA/QC inspection activities during the heat exchanger capacity upgrade project at PT Pertamina RU VI Balongan, including observing the modification of the inlet nozzle from 16 to 18 inches. Involved in understanding technical inspection procedures together with the vendor’s QA/QC team, as well as verifying technical documents such as the MDR and conducting FAT. Participated in hydrotest and pneumatic pressure testing according to ASME standards, focusing on venting and draining point arrangements, instrument calibration, and gradual pressure increase. This experience strengthened my understanding of ASME, AWS standards, and the implementation of the Ministry of Energy and Mineral Resources Regulation No. 32 of 2022 in the field.
PT Kilang Pertamina International – RU VI Balongan
Internship / Project Period
1 March 2022 / 30 Apr 2022
Organizational Structure of PT KPI – RU VI Balongan
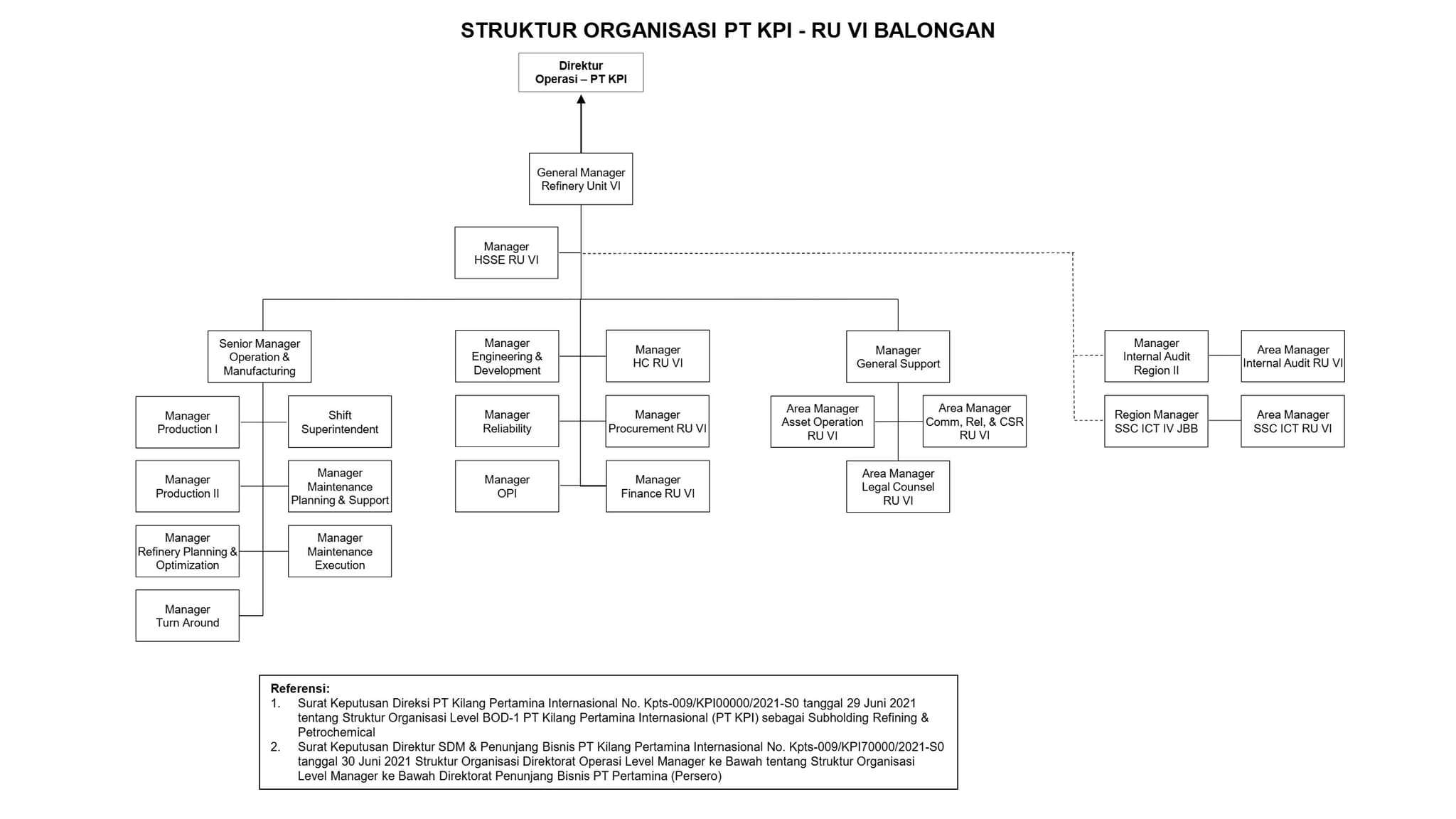
Activities during the Internship:
- Preparing the inspection procedure for Heat Exchanger HE 11-E-102.
- Conducting on-site fabrication process for unit HE 11-E-102.
- Observing the Non-Destructive Testing (NDT) process.
- Observing the welding process of the nozzle and its connection to the HE shell.
- Measuring the shell diameter in the final stage to ensure no deformation occurred.
- Testing the welding joints using hydrotest or pneumatic test; considering non-destructive procedures, the pneumatic test was used on-site.
- Inspecting the dimensions of the welding joints and the entire HE unit.
- Calculating the remaining thickness due to corrosion and evaluating the operational feasibility of the HE based on API 510 standard.
- Preparing a report comparing the dimensional change of the inlet shell nozzle from 16 inches to 18 inches.
- Drafting a conclusion based on the inspection methods used to estimate the service life of the Heat Exchanger.
Inspection And Test Plan For Heat Exchangers
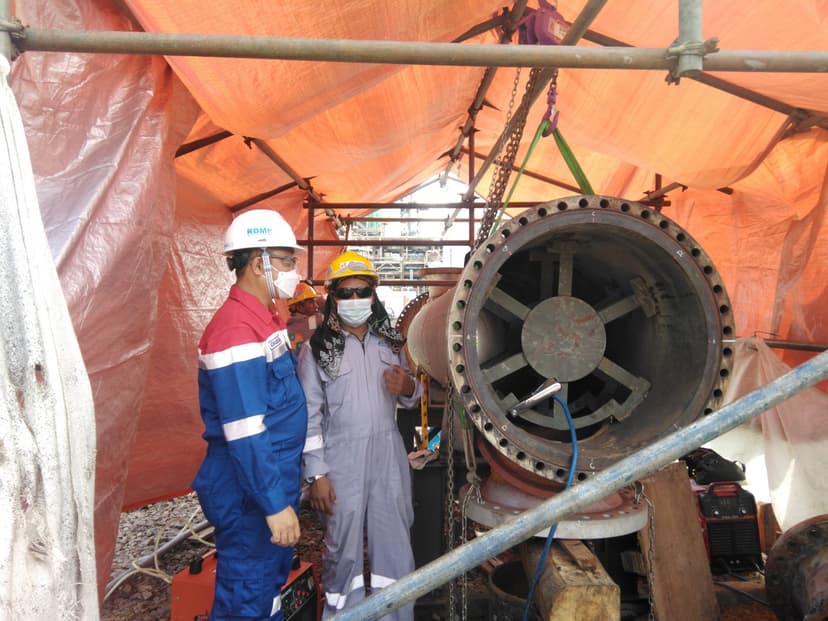
The inspection and testing plan will cover a variety of inspection and testing tasks. For example, Destructive Testing (DT) may be carried out during the early phase of the project to ensure that the material possesses adequate properties and to detect potential leaks in components such as flanges, vessels, manholes, shells, and tubes.
Non-Destructive Testing (NDT) is commonly used in projects because it does not damage the tested material. PT KPI frequently applies NDT methods as they preserve the material’s shape and integrity, which is crucial for long-term reliability. The NDT methods implemented by PT KPI include Visual Inspection and Phase Array Ultrasonic Testing (PAUT).
Inspection Process Stages for HE 11-E-102
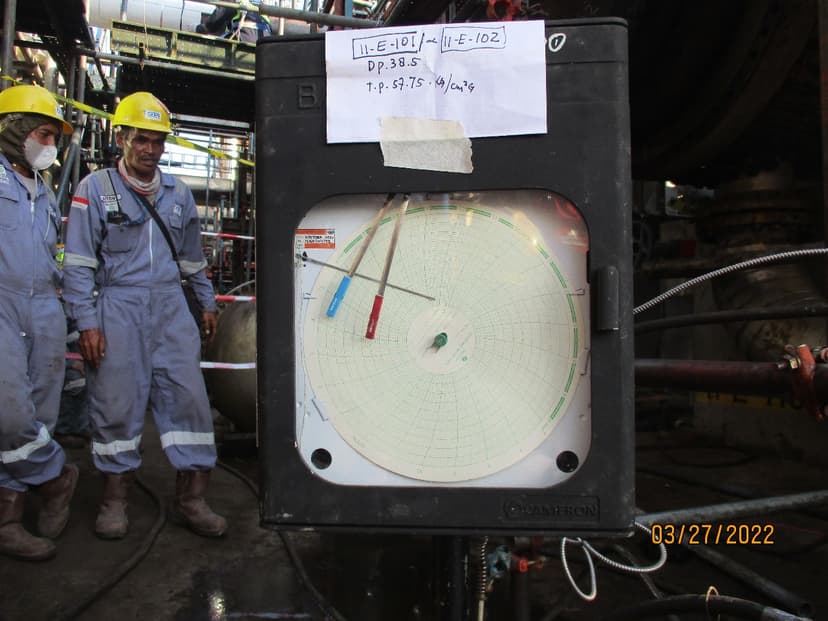
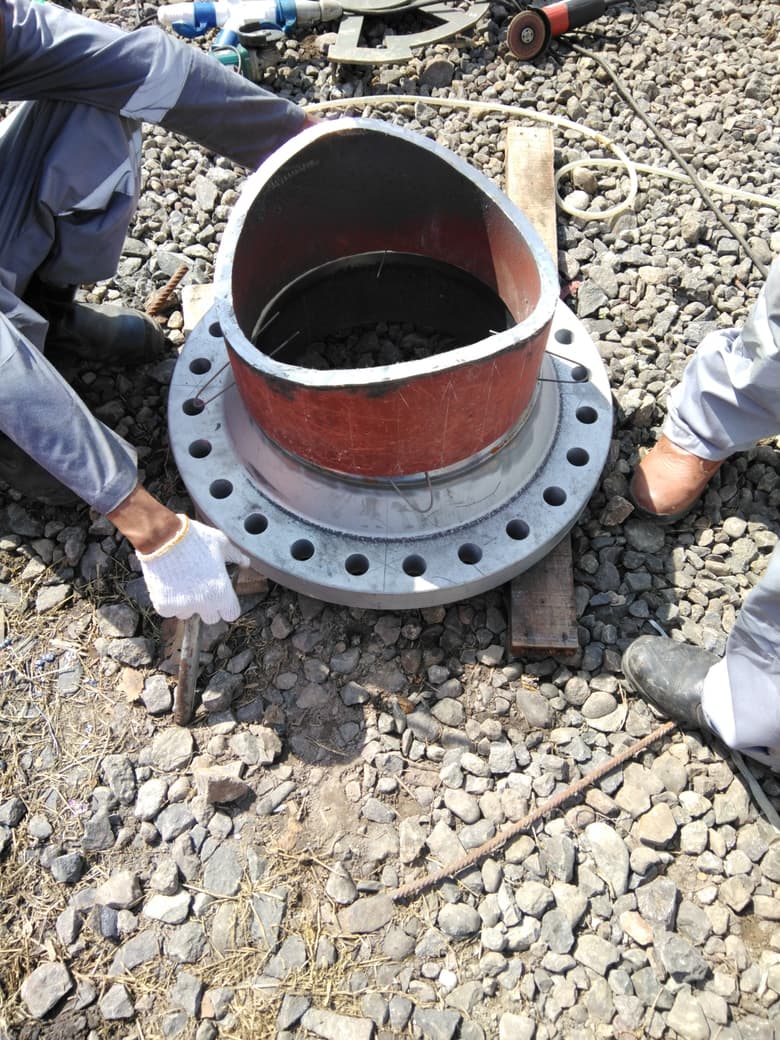
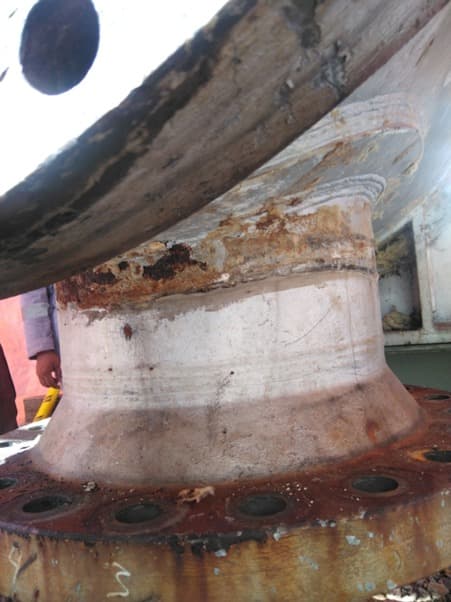
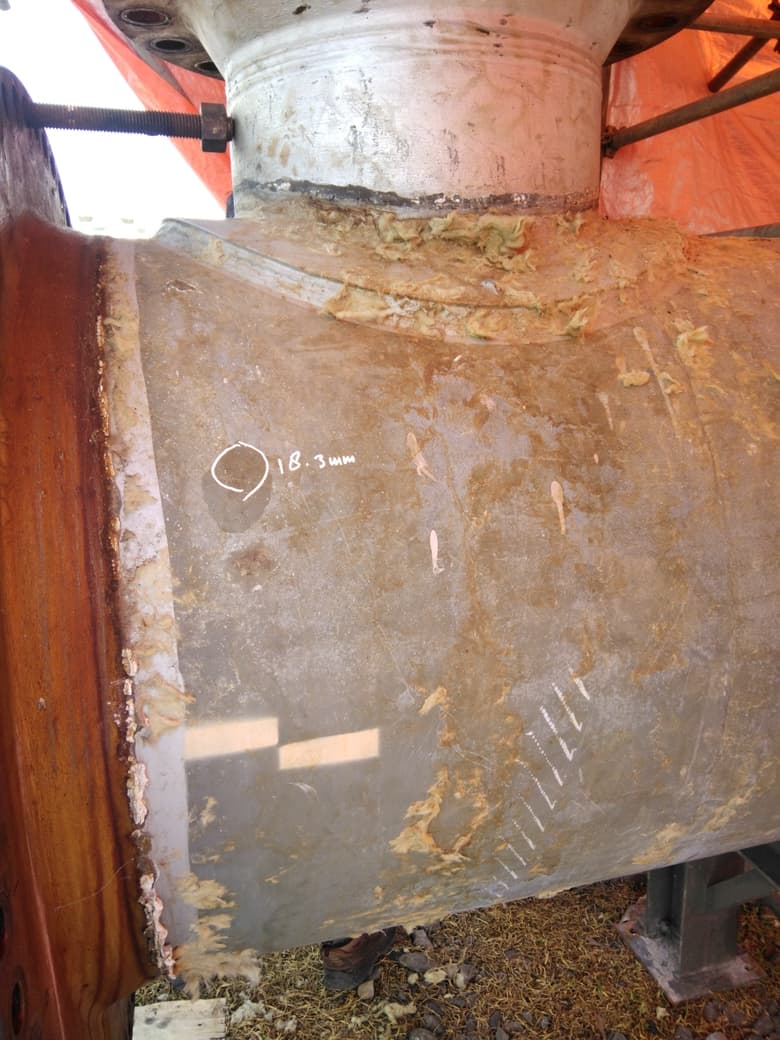
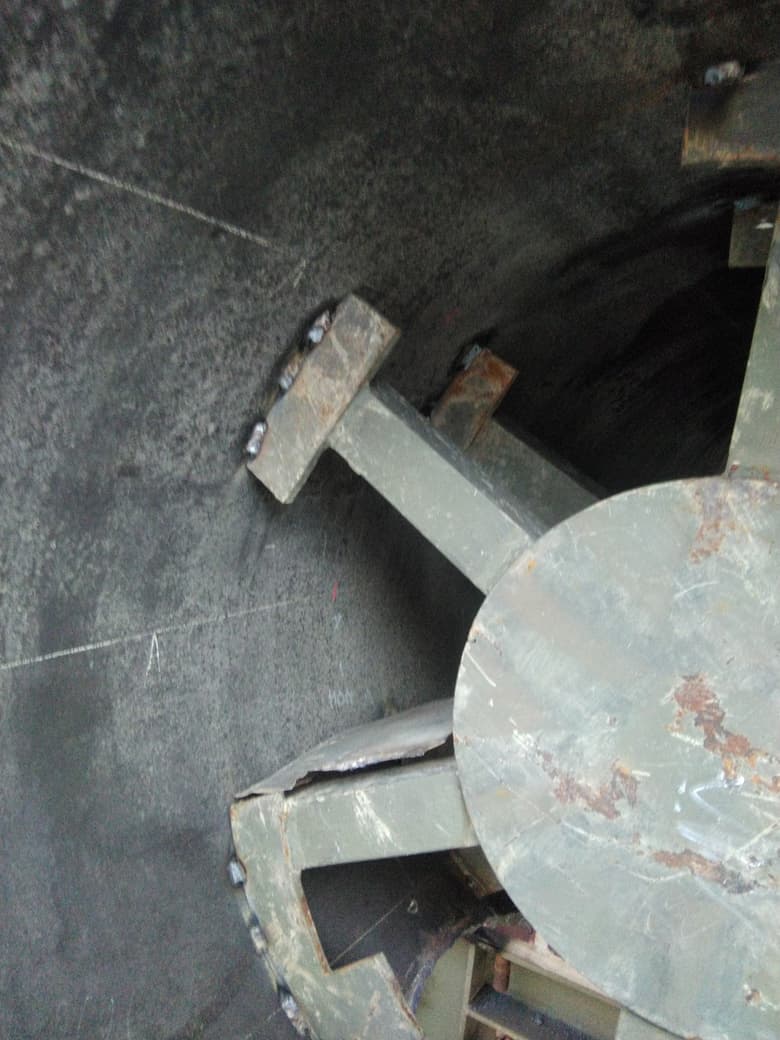
The inspection and testing plan will cover a variety of inspection and testing tasks. For example, Destructive Testing (DT) may be carried out during the early phase of the project to ensure that the material possesses adequate properties and to detect potential leaks in components such as flanges, vessels, manholes, shells, and tubes.
Non-Destructive Testing (NDT) is commonly used in projects because it does not damage the tested material. PT KPI frequently applies NDT methods as they preserve the material’s shape and integrity, which is crucial for long-term reliability. The NDT methods implemented by PT KPI include Visual Inspection and Phase Array Ultrasonic Testing (PAUT).
Dimensional inspection involves several stages, including:
- Visual inspection of the inner shell using measuring instruments such as roundness measurement tools, dial gauges, and others.
- Measuring the shell thickness to ensure it meets or exceeds the minimum allowable limit.
- After welding on the inlet section, Non-Destructive Testing (NDT) is conducted, consisting of Penetrant Testing (PT) and Phased Array Ultrasonic Testing (PAUT).
Following the completion of these three stages on the shell, tubes, and final test pressure, a Hydrostatic Test is performed in accordance with the hydrostatic test procedures established by PT PERTAMINA (Persero).
Several key variables influence the minimum thickness measurement, including size, shape, type of exchanger, material, and manufacturing method. These factors are assessed by comparing measurement differences over time, expressed in millimeters or inches per year.
Measurement Results and Dimensional Inspection Evaluation
Measurements were conducted using tools such as dial gauge, roundness measurement, taper gauge, and welding gauge, in accordance with dimensional testing standards in the oil and gas industry.
The inspection includes:
- Shell Thickness Measurement
Measurements are carried out to ensure there is no thinning below the minimum thickness limit according to technical specifications. The results are compared with design standards and used to evaluate wear due to long-term use. - Visual and Geometrical Inspection
Visual inspection and shell roundness checking using roundness measurement tools are conducted to detect potential deformation. The measurements show that the shell dimensions remain within design tolerance limits, and no signs of deformation or misalignment were found that could affect heat transfer performance or the structural integrity of the equipment. - Post-Welding Testing
After the welding process on the inlet section, NDT methods such as Penetrant Testing (PT) and Phased Array Ultrasonic Testing (PAUT) were conducted. These inspection results are used to assess the quality of the welds and ensure there are no defects in the weld output. - Hydrostatic Test
This test is carried out as the final stage to evaluate the pressure resistance of the Heat Exchanger (HE) system. The testing process follows the official procedure of PT PERTAMINA (Persero), and the results are used to determine whether the equipment meets operational feasibility requirements. All measurement data is analyzed and compiled into a report to assess compliance with final specifications and to provide recommendations for repair or component replacement if necessary.
Inspection Data Sheet for Shell and Channel of HE 11–E–102

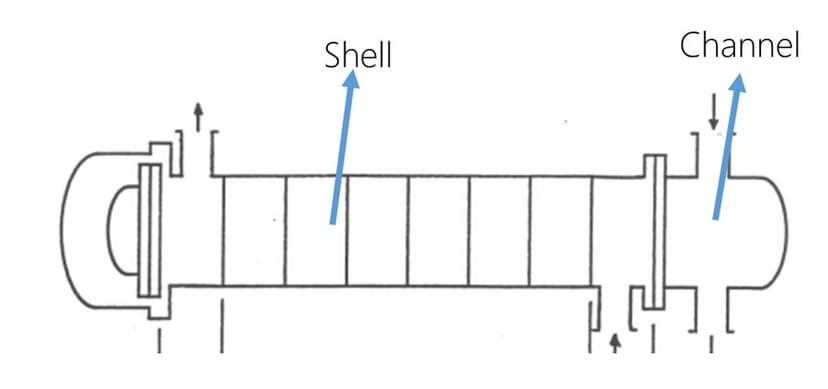
Corrosion Rate and Remaining Life Calculation
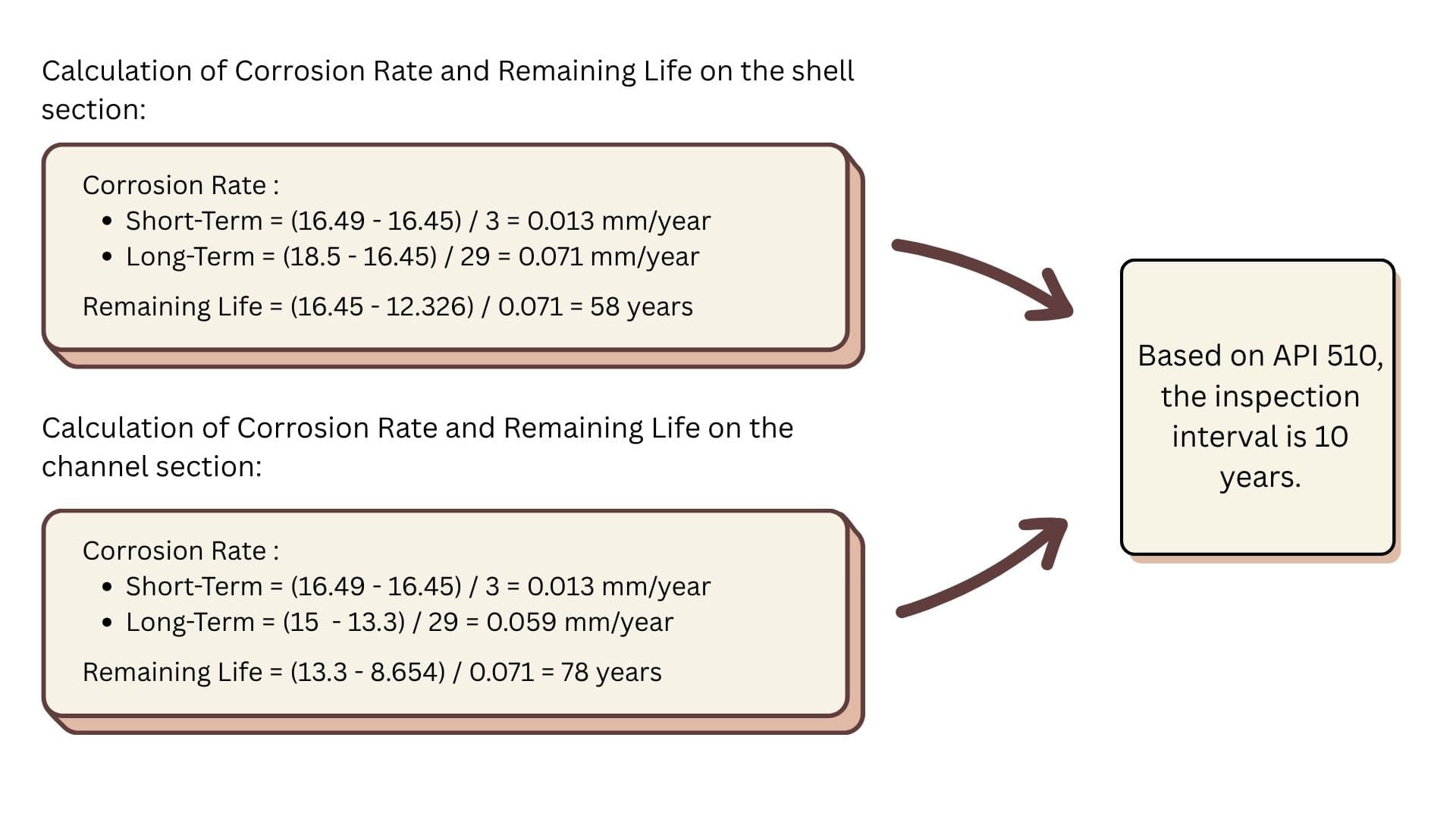
Measurement Results of Heat Exchanger 11–E–102
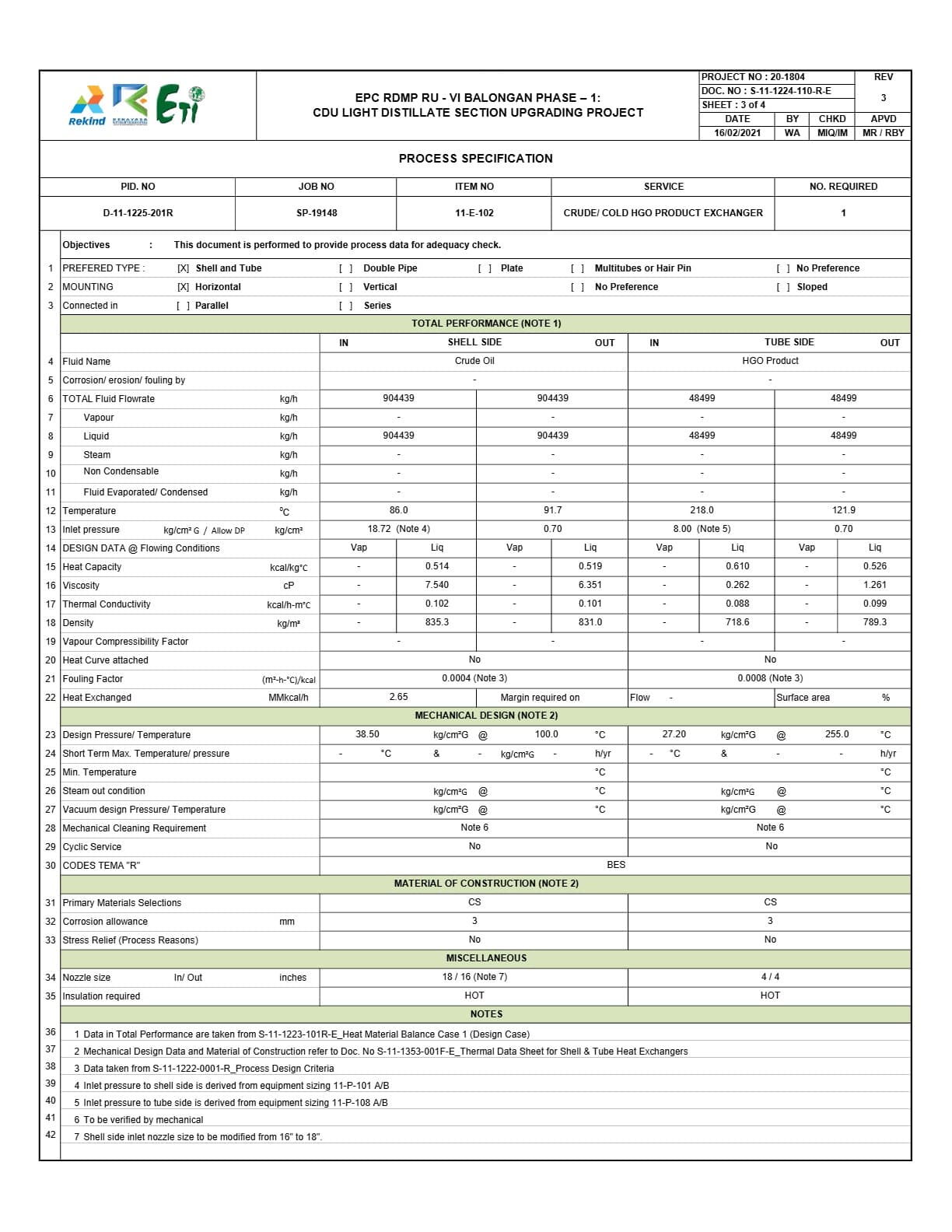
The calculation was performed using HTRI software developed by the Tubular Exchanger Manufacturers Association (TEMA). This software is highly useful for accurately simulating and verifying the performance of heat exchangers.
Comparison of Inlet Shell Nozzle Modification Using HTRI Software
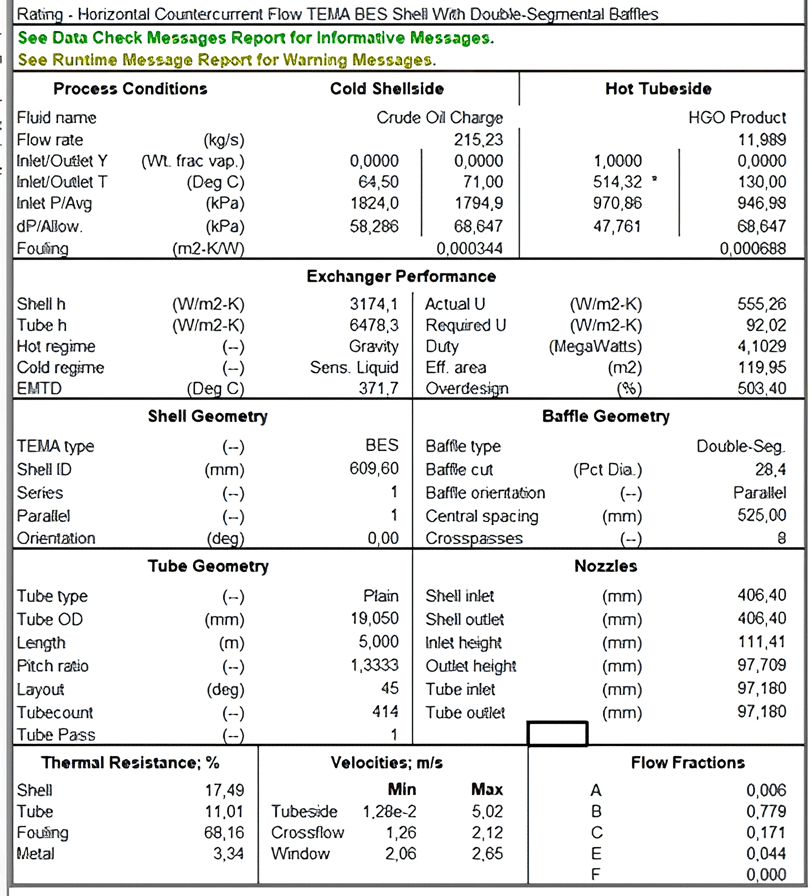
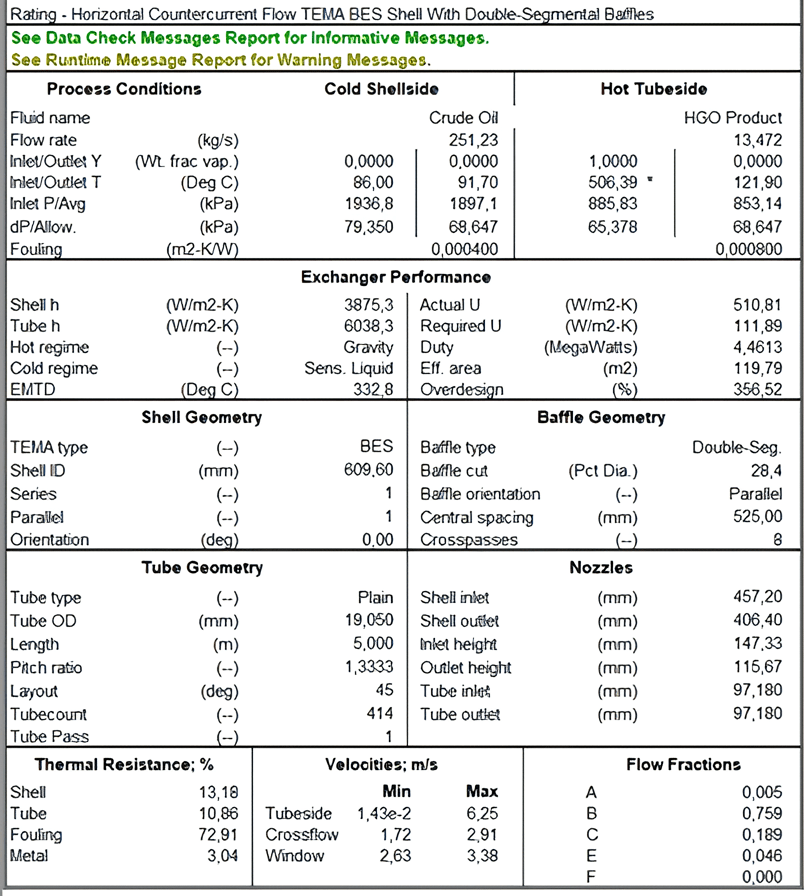
Results of Inlet Shell Nozzle Modification Comparison from 16 Inches to 18 Inches Using HTRI Software
The comparison results of the inlet shell nozzle modification from 16 inches to 18 inches using HTRI software indicate a heat transfer capacity increase of 8.7%, a flow rate improvement of 17%, and a 22% increase in the shell-side heat transfer coefficient. However, the average temperature effectiveness decreased by 10%, indicating a trade-off between capacity enhancement and thermal efficiency.